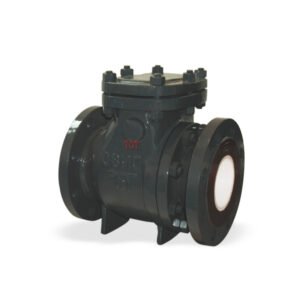
Ceramic Swing Check Valve
Ceramic swing check valve is a check valve used to prevent pipeline backflow, especially for pipelines that convey corrosive or high solid particle content media such as slurry, ash or chemical mixtures.
Contact us now for market competitive prices.
Description
The internal seals and fluid contact parts (valve disc and valve seat) of the ceramic swing check valves we produce are made of high-quality zirconium oxide (ZrO₂) or aluminum oxide (Al₂O₃) ceramics to meet your harsh conveying system working conditions.
If your system handles slurry, solid particles, or aggressive flow conditions, you know that traditional metal check valves often fail prematurely. Our ceramic swing check valve offers a long-lasting solution, purpose-built to prevent backflow in abrasive, erosive, and medium-corrosive applications.
Designed with advanced ceramic technology, this valve is ideal for use in power plants, mineral processing, chemical pipelines, and pneumatic conveying systems — anywhere where flow direction control must be combined with high wear resistance.
Whether you’re a procurement engineer or a systems integrator, we’re ready to support your project with fast response, customization options, competitive price and reliable international shipping.
Key Benefits at a Glance
– Advanced Ceramic Internals: The valve disc and seat are lined with high-purity zirconia or alumina ceramic, offering exceptional hardness and resistance to wear, corrosion, and high-velocity erosion.
– One-Way Flow with Secure Shut-Off: The swing-type check mechanism allows free flow in the forward direction and automatically closes when flow reverses, protecting pumps, pipes, and critical equipment.
– Low Pressure Loss, Full Flow Design: Engineered for minimal resistance, the valve provides smooth, unobstructed flow while ensuring reliable backflow prevention.
– High Durability in Harsh Environments: Performs reliably in slurry pipelines, ash handling, and chemical dosing systems where conventional valves wear out quickly.
Main Component Materials
Number | Name | Material | Number | Name | Material | Number | Name | Material |
---|---|---|---|---|---|---|---|---|
1 | Body | WCB | 4 | Rocking Arm | Graphite | 7 | Nut | Graphite |
2 | Stem | WCB | 5 | Washer | – | 8 | Washer | WCB |
3 | Disc | WCB | 6 | Stud | Q235 | 9 | Bonnet | – |
Main Appearance and Connection Dimensions (Unit: mm)
Size | PN | L | D | D1 | D2 | C | H | n-Φd | |
---|---|---|---|---|---|---|---|---|---|
DN | In | ||||||||
100 | 4″ | 10 | 292 | 220 | 180 | 165 | 22 | 270 | 8-18 |
125 | 5″ | 330 | 250 | 210 | 184 | 22 | 280 | 8-18 | |
150 | 6″ | 356 | 285 | 240 | 211 | 24 | 290 | 8-22 | |
200 | 8″ | 495 | 340 | 295 | 266 | 24 | 345 | 8-22 | |
250 | 10″ | 622 | 395 | 350 | 319 | 26 | 412 | 12-22 | |
300 | 12″ | 698 | 445 | 400 | 370 | 26 | 468 | 12-26 | |
350 | 14″ | 787 | 505 | 460 | 429 | 30 | 524 | 16-26 | |
400 | 16″ | 914 | 565 | 515 | 480 | 32 | 524 | 16-30 | |
100 | 4″ | 16 | 292 | 220 | 180 | 210 | 22 | 270 | 8-18 |
125 | 5″ | 330 | 250 | 210 | 240 | 22 | 280 | 8-18 | |
150 | 6″ | 356 | 285 | 240 | 265 | 24 | 290 | 8-22 | |
200 | 8″ | 495 | 340 | 295 | 320 | 26 | 345 | 12-22 | |
250 | 10″ | 622 | 405 | 355 | 370 | 26 | 412 | 12-26 | |
300 | 12″ | 698 | 460 | 410 | 429 | 26 | 468 | 16-26 | |
350 | 14″ | 787 | 520 | 470 | 480 | 30 | 524 | 16-26 | |
400 | 16″ | 914 | 580 | 525 | 480 | 32 | 524 | 16-30 |
Fast Response & Competitive Pricing Start Here
* We are not just providing simple quotes but experts in selection, calculation, and drawing.